On a typical pharmaceutical production line, over 10,000 tablets pass through quality control stations every hour. Imagine searching for defects in this endless stream for 8 hours straight, without stopping the conveyor belt. How many hours would it take before your eye becomes fatigued? Would you still be able to spot subtle imperfections like microscopic cracks in tablet coatings or slight color variations that could indicate contamination?
No wonder that manual inspection is becoming a relic of the past: 58% of manufacturing firms are planning computer vision implementation, with 77% acknowledging its necessity for smarter, more efficient production according to a Deloitte survey.
It’s no surprise – in times of tariffs, rising energy and raw material costs, and the specter of recession, any reputational damage costs significantly more, and this must be considered when defective products reach the market. Organizations typically spend 15-20% of sales revenue on quality-related costs, with some spending as much as 40% of total operations.
The potential is enormous – AI-based visual inspection can increase defect detection rates by up to 90% compared to human inspection, with productivity increases of up to 50% possible through advanced image recognition techniques.
However, the reality is sobering: 80% of AI projects in organizations fail according to research from Rand Corporation, with Gartner reporting only 30% of AI projects move past the pilot stage. This stark contrast between potential and reality underscores why choosing the right implementation partner with deep manufacturing expertise is critical for success.
In this article, we break down computer vision use cases and common challenges that come along with such projects. We also share good practices that may secure a successful computer vision implementation in your company.
High-stakes industries: where computer vision matters most
Today, computer vision in manufacturing is standard across many industries, especially those subject to stringent regulations. Pharma and food manufacturing is where the potential to enhance efficiency is the highest.
Computer vision in pharma manufacturing industry
In the pharmaceutical manufacturing industry, where maintaining a sterile environment is essential, and manufacturing plants are responsible for patient safety while facing the risk of high regulatory fines, such applications have long been popular. Overall, pharmaceutical companies are not hesitant to adopt AI and AI agents in manufacturing. In fact, according to a 2024 global survey by Intuition Labs, almost seven out of ten pharmaceutical companies reported already using AI.
Computer vision is a key component of these implementations, supporting tasks such as tablet inspection, packaging verification, and contamination detection. It helps companies automatically verify, for example, whether packaging labels are legible, blister packs are intact, vials and ampoules are free from particulate contamination, and products have no quality defects.
These data feed into quality control systems, which often incorporate generative AI for more accurate results, as is the case with Merck. Novo Nordisk also employs similar solutions in its manufacturing facilities.
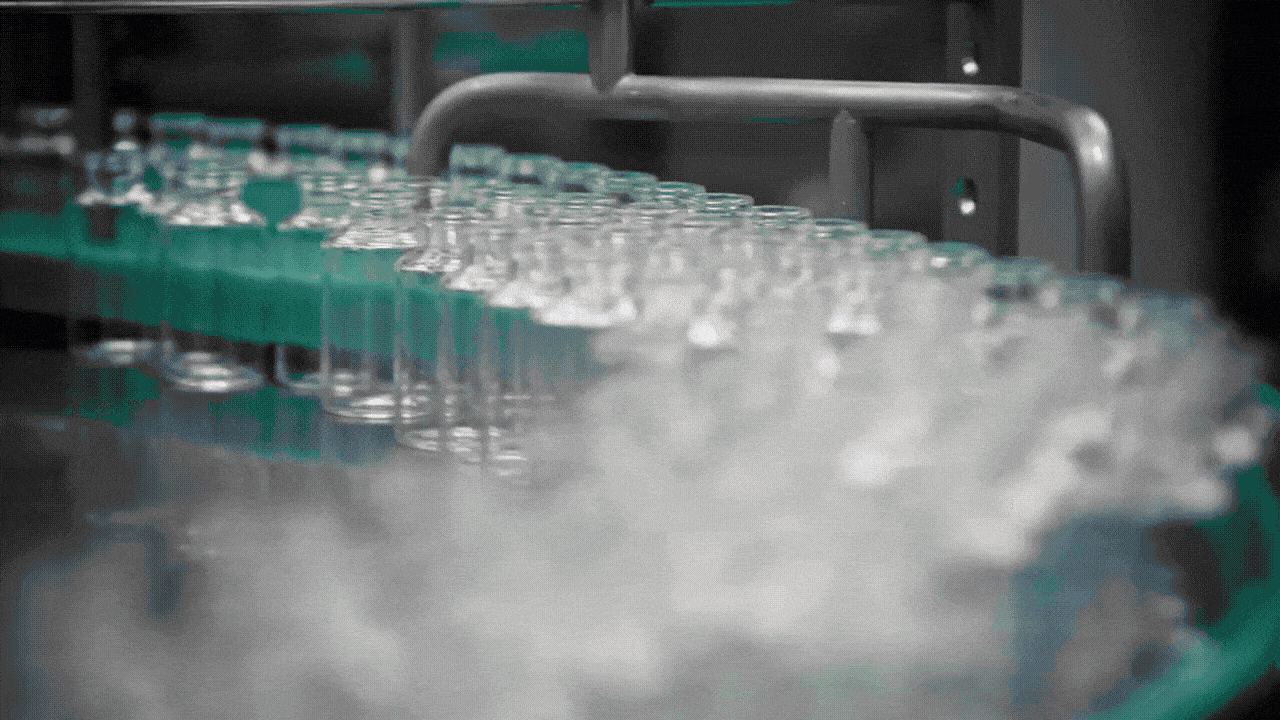
Computer vision in food manufacturing and foodtech
Even on highly automated food production lines, little missteps can still slip through. But you will probably agree that missing cookies in a pack, mixed pasta shapes, discolored vegetables, or sugar cubes of the wrong size are exceptionally rare. That’s no accident – computer vision systems are increasingly used to uphold strict food safety standards, from HACCP protocols to FDA regulations, and ensure consistent quality.
In the food manufacturing sector, computer vision software development plays a pivotal role in multiple critical scenarios: foreign object detection, freshness or spoilage assessment, and packaging integrity checks. These use cases safeguard consumer health, shield brand reputation, and help avoid costly regulatory penalties.
Take, for example, Italian company Specialvideo, which employs computer vision to inspect pizzas in real time – detecting toppings, verifying placement, and identifying contaminants at speeds under 250 ms per pizza, achieving over 95 % accuracy. Another case is Sunsweet Growers, the world’s largest prune distributor, where a computer vision system automatically grades and detects defects in prunes at collection sites around the globe.
The global giants, like Kraft Heinz, are also using computer vision in manufacturing processes to drive excellency. One of their standout use cases is all about a perfect pickle: visual assessment of the cucumbers, including their length and density, enables them to ensure the optimal crunch.
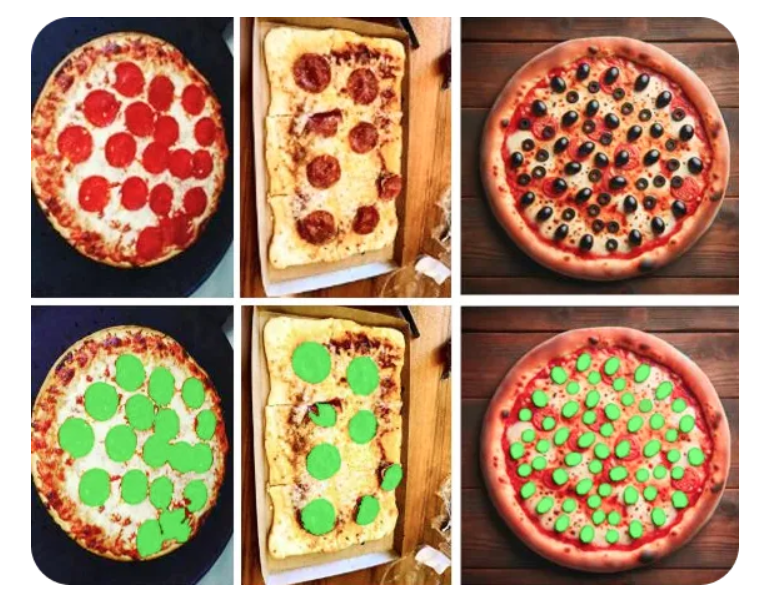
Yet food products bring technical challenges that pharmaceutical lines typically don’t: variability in shape, color and texture, dynamic lighting and environmental conditions, and throughput requirements of many items per second. Systems must adapt to different product appearances – whether a ripe tomato, an almond flake, or a loaf of bread—under changing conveyor speeds, varying illumination, and humidity or dust in the environment.
Regulatory frameworks like HACCP and FDA mandates demand rigorous controls. Computer vision supports this by automatically:
- detecting foreign objects like plastic, metal, or stray debris
- assessing freshness indicators (such as color shifts or mold presence)
- verifying packaging defects – ripped seals, wrong labels, or incorrect fill levels.
Together, this technology addresses the core risk factors in food manufacturing: protecting consumer health, maintaining brand trust, avoiding recalls and fines, and reducing waste through early detection of anomalies.
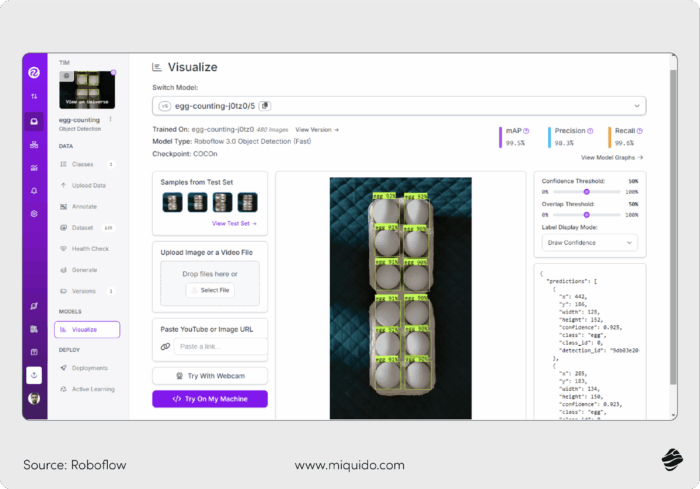
Manufacturing computer vision – essential use cases
From computer vision based maintenance to defect detection and streamlining inventory management, here is how manufacturers can make the most of this technology.
Quality control and inspection
A single misprinted label or a discolored tablet may seem minor, but when repeated across thousands of units, the damage to a pharmaceutical brand’s reputation – and bottom line can be significant. Imagine catching every flawed item before it reaches packaging, without slowing down production or relying on fatigued human inspectors.
In pharmaceutical manufacturing processes, ensuring product integrity is non-negotiable. This is where computer vision technology delivers measurable ROI. For example, defect detection systems can automatically remove items with texture irregularities, off-spec coloration, or surface cracks, leading to reduced scrap rates and fewer customer complaints. Advanced vision systems can detect material inconsistencies invisible to the human eye, improving quality inspection accuracy and maintaining GMP compliance.
Computer vision models also verify label presence, orientation, and barcode readability with precision, which is critical for meeting FDA traceability mandates. With fewer returns and stronger compliance assurance, these systems quickly pay for themselves. Effective deployment requires strategic lighting, precise camera placement, and seamless integration with rejection mechanisms to support high-throughput quality inspection.
A reliable software partner brings deep learning expertise, helping manufacturers interpret visual data with tailored computer vision models suited to the exact product and environment. With domain-specific experience, they streamline implementation and minimize operational disruption.
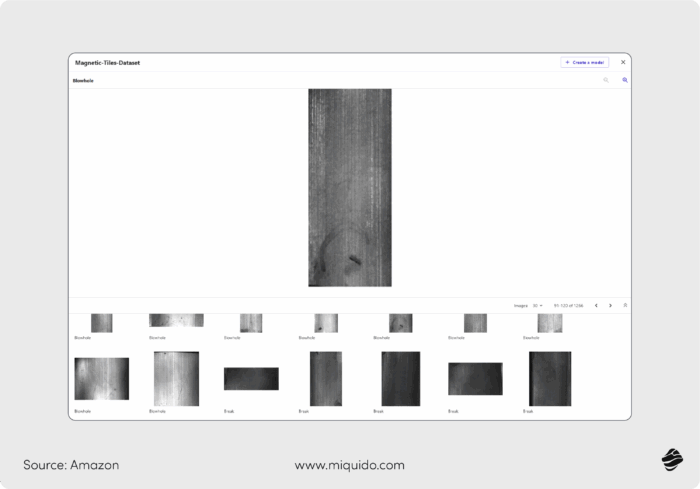
Production line optimization
Thousands of small food products – cookies, berries, or candies – move along a conveyor every minute. Manually tracking or sorting them by appearance or defects is nearly impossible. Even a few seconds of delay or misalignment can cascade into hours of lost production and waste.
In food production processes, operational efficiency depends on fast, accurate classification and flow control. Computer vision technology plays a central role.
- Automated sorting systems use computer vision techniques to grade items by size, shape, or texture – removing discolored or misshaped goods in real-time, which improves shelf appeal and reduces post-distribution recalls.
- Object counting powered by computer vision models supports inventory accuracy and real-time production monitoring.
- Alignment detection prevents bottlenecks by ensuring items are properly oriented before packaging.
- Jam prevention systems use visual data and AI alerts to intervene early when components are misaligned, avoiding costly pileups.
These computer vision applications lower downtime, cut waste, and increase throughput. Implementation success hinges on high-speed imaging, accurate belt synchronization, and real-time processing capabilities.
An experienced partner ensures that computer vision enables manufacturers to embed intelligent control into every part of the line, with high-performance models optimized for real-world variability and lighting conditions.
Predictive maintenance and equipment monitoring
When a small crack forms on a high-value machine, the clock starts ticking. Without early detection, it can escalate into full equipment failure, causing unplanned downtime that costs thousands per hour. Manual checks are too infrequent to catch every early-stage fault.
Computer vision models make predictive maintenance in manufacturing highly scalable and proactive.
- Vision-based systems monitor equipment surfaces for rust, cracks, or deformations, extending the life of machines and preventing catastrophic breakdowns. These systems provide visual data inputs for early warning dashboards, allowing engineers to schedule targeted repairs instead of broad maintenance sweeps.
- Deep learning algorithms improve accuracy over time, reducing false positives and identifying subtle visual cues before they lead to failure. This dramatically cuts downtime and maintenance costs.
- Continuous monitoring with edge computing devices allows for seamless integration into existing systems.
A trusted implementation partner ensures compatibility with your infrastructure and supports model training to match specific machine types and wear patterns. There is no better path to long-term savings and equipment reliability.
Safety and compliance monitoring
A fall on the production floor isn’t just a medical emergency. It can lead to investigations, lawsuits, or halted operations. Spotting such incidents in real time, without violating privacy or interrupting workflows, is a delicate balance.
In compliance-heavy environments, workplace safety and monitoring are top priorities. Computer vision techniques enable fall detection by distinguishing involuntary accidents from actions like kneeling, improving response times and reducing injury severity.
- PPE compliance tools confirm the presence of required gear – helmets, gloves, masks – without human supervision, reducing oversight costs and improving adherence.
- Zone monitoring systems track unauthorized access to sensitive areas, helping enforce access policies and prevent safety breaches.
These tools support regulatory compliance, lower liability risks, and protect workers. Implementation requires real-time response capability, camera calibration, and employee buy-in to avoid resistance and privacy concerns.
The data problem: A core obstacle to AI in manufacturing
Let’s step back in time and imagine that AI solutions are still a distant future. On the production line, products are manually verified for defects. Among the workers, one stands out with an exceptional eye for detail.
Where does this effectiveness come from? Most often, it’s the result of years of experience, pattern recognition developed through seeing thousands of products, and the ability to distinguish subtle variations that indicate quality issues – the same process through which computer vision algorithms gain their effectiveness.
Artificial intelligence works in a similar way – except that when this exceptionally skilled worker loses focus or simply gets used to monotonous processes and loses effectiveness, AI will continue to operate with equal precision.
However, this doesn’t mean that adopting computer vision in manufacturing is a solution that presents no challenges to manufacturers.
Why manufacturing data is hard to get right
The first and most fundamental challenge is data scarcity. Most datasets must be built from scratch – manually collected and preprocessed. This process can take months or even years, depending on the complexity of the production line.
Consider a pharmaceutical tablet production line: collecting sufficient examples of various defect types (cracks, discoloration, incorrect embossing) while maintaining production schedules requires careful coordination and can extend project timelines by 6-12 months.
Privacy and IP concerns create another significant barrier, as confidentiality fears prevent data sharing between firms. The financial consequences can be severe – leaked production data or quality control processes can result in competitive disadvantage worth millions of dollars, while regulatory bodies like the FDA or EMA may impose additional scrutiny if data handling protocols are compromised.
Domain specificity adds another layer of complexity, as each production line requires unique, context-aware datasets. A computer vision system trained to detect defects in automotive paint finishes will be completely ineffective for identifying contamination in sterile pharmaceutical vials – the lighting conditions, surface characteristics, defect types, and even the definition of “acceptable quality” are entirely different.
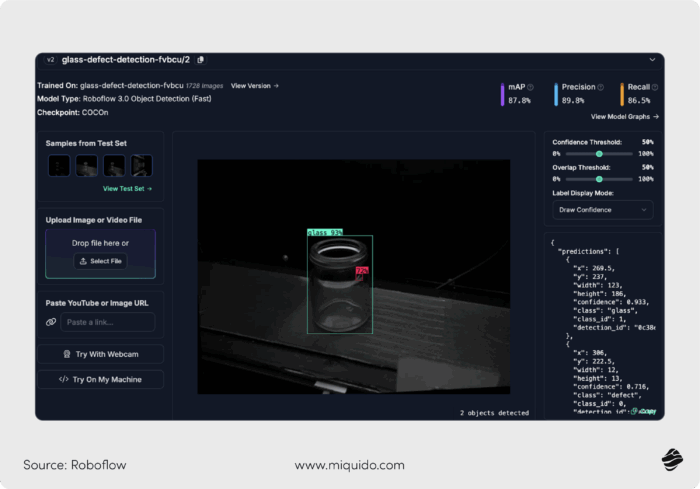
Common dataset challenges
These fundamental issues cascade into a series of interconnected challenges that can derail even well-intentioned AI initiatives:
Low availability of relevant, labeled, and high-quality data remains the primary bottleneck. Unlike consumer applications where millions of images are readily available, manufacturing datasets require expert annotation and domain-specific knowledge to label defects correctly.
Siloed data systems and lack of governance frameworks create additional friction. Quality control data might live in one system, production metrics in another, and maintenance logs in a third, making it nearly impossible to create comprehensive datasets that reflect real-world conditions.
Shortage of skilled AI talent with manufacturing domain knowledge compounds the problem. Data scientists who understand neural networks may not grasp the nuances of pharmaceutical compliance or automotive quality standards, while manufacturing experts may lack the technical skills to properly structure and prepare data for AI systems.
Incompatibility with edge deployment requirements presents yet another hurdle. Manufacturing environments demand low latency and often have limited compute resources, but many AI models are designed for cloud environments with abundant processing power.
No built-in model adaptability means that models degrade without retraining on new data. As production lines evolve, new defect types emerge, or quality standards change, AI systems become less effective over time.
Non-standardized data formats, units, and semantics impede integration and reuse. What one system calls a “major defect” might be classified as “minor” in another, making it difficult to leverage existing datasets for new applications.
We could try to break down how to solve each of these challenges one by one, but the reality is that tackling them in isolation is a never-ending uphill battle. A seasoned manufacturing software provider already brings what’s needed: robust data preprocessing pipelines, trusted annotation workflows, proven model architectures tailored for edge deployment, and most importantly, deep domain expertise to identify which defects actually matter for your specific industry and regulatory requirements.
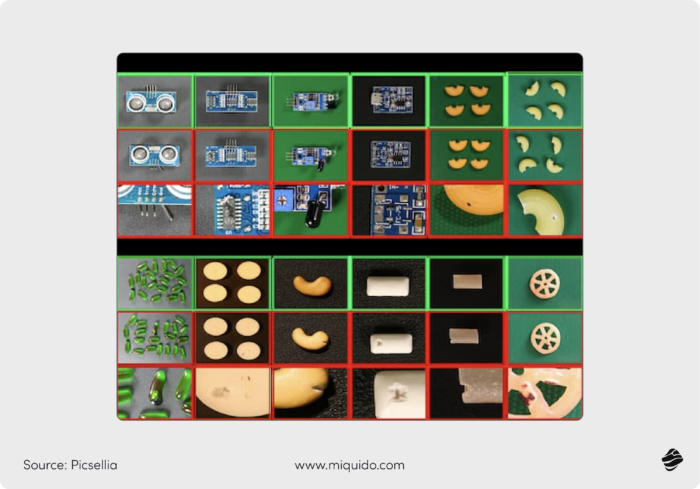
Solving the data challenge: Practical recommendations
You’ve likely heard the promise of AI, but without a strong data foundation, initiatives stall, costs balloon, and your teams lose confidence. Worse, fragmented data strategies leave your organization vulnerable to inefficiency, compliance risks, and poor decision-making. But there is a way to avoid that and pave a way to quick ROI. Here are the good practices we use as a roadmap.
Break silos to prevent data fragmentation and misuse
Promote collaboration across departments and encourage data democratization. Clear ownership and open access (with guardrails) make your organization’s data assets more actionable and trusted.
Secure your data with smart governance to avoid future liability
Define strict protocols for how data is shared, accessed, and stored – particularly when working with sensitive production or personnel data. This is critical not just for compliance, but for long-term scalability.
Invest in MLOps to future-proof your AI initiatives
Enable CI/CD/CT pipelines so AI models can continuously learn, adapt, and improve. MLOps transforms experimental code into production-ready pipelines that actually deliver business value in machine learning operations.
Bridge the AI talent gap without hiring from scratch
Rather than overextending internal teams, either upskill key domain experts or partner with AI-focused vendors who understand your industry and can translate business goals into working models. This is especially important in machine learning-heavy efforts like computer vision projects, which often require tight integration with real-world manufacturing tasks and infrastructure.
The computer vision market is growing rapidly, but successfully implementing computer vision isn’t just about adopting new tech, but also aligning use cases with measurable business impact. From defect detection to workplace monitoring, machine vision is becoming central to quality, safety, and productivity.
Building a sustainable AI strategy and efficient machine vision systems takes more than boardroom vision – it requires deep technical execution, tight alignment, and expert capacity that most teams simply don’t have time to source or build from scratch. A trusted software partner can close that gap with the right talent and tools, fast. Whether you are looking to enhance safety or implement AI manufacturing quality control, we can support you with our expertise in industry 4.0 software development. You can also enhance the efficiency of the computer vision system with our generative AI Kickstarter framework, saving 60% costs of typical development.