Imagine a factory filled with humming machines, tight schedules, and teams coordinating at every step, yet all decision-making runs through disconnected spreadsheets and outdated reports. That’s what operations look like without digital manufacturing technologies. Data may exist in abundance, but without integration, it’s like fuel locked in barrels – powerful, but inaccessible.
Forecasting errors, bottlenecks, manual data entry mistakes, and unnecessary labor costs quickly follow. In contrast, digital manufacturing technologies link systems across operations, streamlining processes, enhancing forecasting accuracy, and minimizing downtime. The payoff? Smarter decisions, fewer errors, and leaner, more agile operations.
Is Europe leveraging this potential? We crunched the numbers to find out. Our analysis dives into how EU countries are adopting digital manufacturing technologies – those that unify operations from the shop floor to the supply chain, and what this means for the future of the sector.
Digital transformation in the manufacturing industry: A strategic necessity
In 2024, the European manufacturing sector is undergoing a dynamic evolution, where the integration of business processes determines companies’ competitive positions. Market leaders such as Germany and the Netherlands are implementing comprehensive supply chain management solutions,
On the other hand, Poland and other Central and Eastern European countries still struggle with challenges stemming from a lack of cohesive digitalization strategies. Where does the problem lie, and what actions should be taken? How do the companies adapt computer systems to manufacturing industry needs? The answer, as always, is in the data. Let’s dive into the data.
Digital integration in EU – who is the leader of innovation?
As you’ll see from the statistics below, there are significant differences between various EU regions in the pace of digital technology adoption for different types of improvements.
E-Invoicing: do manual processes still have a place?
Manual invoice processing in the manufacturing industry is a clear invitation for problems. Duplicate payments, misfiled documents, and delayed approvals are just a few examples of common issues manufacturers face when they don’t use e-invoicing. In this sector, invoice processing errors can have especially severe consequences due to complex supply chains, high transaction volumes, and the need for precise production scheduling.
Across the European Union, many manufacturers still operate without e-invoicing—though adoption rates vary significantly by region. The further north you go, the more popular e-invoicing becomes. For example, in Germany, the Netherlands, and Sweden, over 90% of companies use fully automated e-invoicing systems.
The picture is different in Central and Eastern Europe. In Poland, for instance, only 68% of companies use e-invoicing, and many still rely on paper invoices. That’s a significant issue – high costs of manual data processing and the risk of errors lead to delays and increased operational expenses.
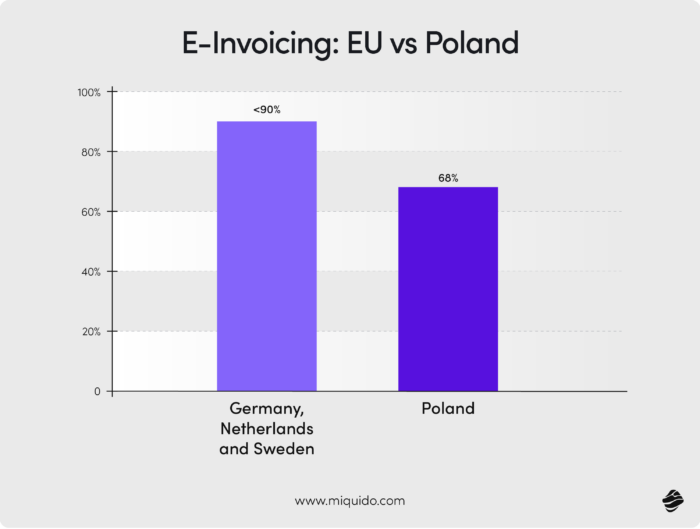
ERP and CRM – optimization tools or unnecessary costs?
An ERP system is a foundational tool for managing data and efficiently planning operations in the manufacturing sector. Its core functions – inventory management, production planning, supply chain coordination, and financial tracking—form the backbone of modern manufacturing processes.
Meanwhile, CRM systems for manufacturing are essential for successful sales and customer relationship management. A CRM enables companies to track customer interactions, manage sales pipelines, and analyze customer data, which directly translates into improved customer retention and revenue growth.
It might seem obvious that every manufacturing company on the market uses both ERP and CRM systems – but statistics tell a different story. Across the European Union, only 78% of manufacturing firms use ERP systems. Just like with e-invoicing, the level of integration drops significantly in Central and Eastern Europe – in Poland, for example, only 52% of companies use ERP solutions.
This gap comes at a high cost. Without ERP, companies operate on incomplete data, losing the ability to respond dynamically to shifting market demands. And without a CRM system, they miss out on the opportunity to build strong customer relationships, personalize their offerings, and drive long-term loyalty.
Business intelligence – data as a key asset
Data is a treasure, but without the right digital tools to extract and refine it, its value remains untapped. In the manufacturing industry, where complex production processes and volatile supply chain dynamics significantly impact operations, implementing Business Intelligence (BI) for real-time data analytics can deliver powerful results. Among the most important benefits are improved decision-making accuracy and greater alignment of production volumes with actual market demand.
Do the EU businesses benefit from this potential in 2025? Scandinavian manufacturers clearly understand the importance of BI: in this region, 80% of production companies use BI for real-time data analysis. Across the Baltic Sea, however, BI adoption drops sharply—in Poland, only 30% of companies use BI, revealing a gap in effective, data-driven strategies. As a result, business decisions may be less accurate, production volumes may miss market needs, and critical services, supply chains, and product opportunities could be lost.
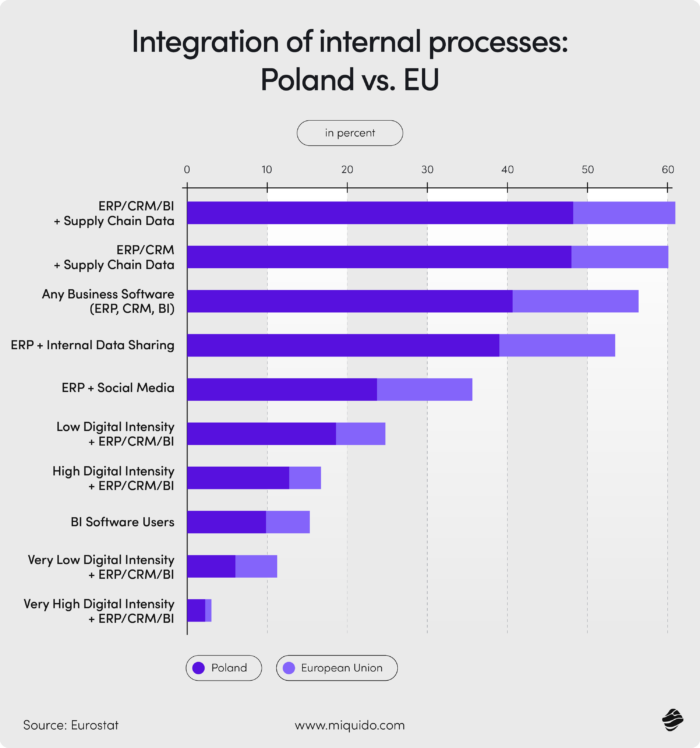
The numbers speak for themselves: companies that have implemented BI report 25% higher profitability and better resource optimization. While deploying these technologies requires some investment in systems and infrastructure, manufacturers are increasingly realizing the immense value they unlock.
In Poland, this shift is already visible in funding trends. Our recent analysis focused on automation in the joinery industry revealed that many joinery manufacturers applied for 2024 grants (Hensfort, Gerda and more) to support the implementation of solutions that link systems and processes, leveraging AI to boost cybersecurity and efficiency.
This is a clear sign that more companies are preparing for the future of digital manufacturing, where digital technology will be at the core of every operational decision.
Integration with clients and suppliers: the key to flexibility
Digital integration is more than just a smooth data flow within an organization. It enables manufacturers to gather, transmit, and process data from external sources, including their entire services, supply chains, and sales channels. This allows companies to react quickly to changes, delays, or unforeseen disruptions. As a result, customers benefit from accurate delivery estimates and better service, while suppliers enjoy faster communication and clearer demand forecasts.
Imagine a scenario where a batch of key components in the manufacturing process gets delayed due to a port closure caused by extreme weather conditions. As a result, the manufacturer cannot complete the next production phase on time, and the customer experiences a delivery delay.
In a traditional setup, resolving this might have involved manual calls, long email threads, and reactive adjustments. With full integration, however, real-time alerts trigger immediate replanning in SCM systems, alternative suppliers are contacted automatically, and customers are proactively notified -greatly reducing the negative impact.
Advanced supply chain management: The smart manufacturer’s weapon
Integrated supply chain management (SCM) systems are a manufacturer’s best defense in today’s volatile market. Instant adaptation to product availability, real-time route tracking updates, automated logistics rerouting, and predictive inventory planning are just a few of the advantages. With such systems, manufacturers can act proactively, preventing both shortages and oversupply, and keeping production processes aligned with demand.
Leading EU manufacturing countries are already setting the pace. In Germany, the Netherlands, and Sweden, over 85% of companies have integrated their SCM with predictive analytics tools. Western and Central Europe are close behind—France, Spain, and Austria show adoption rates between 70% and 80%, although data integration with external partners remains limited.
Further east, the situation is less optimistic. In Poland, 60% of manufacturers use digital SCM tools, but just 30% have AI-powered predictive capabilities in place. In Bulgaria and Romania, less than 50% of companies leverage modern SCM, making them more vulnerable to supply chain disruptions and delays in the entire manufacturing process.
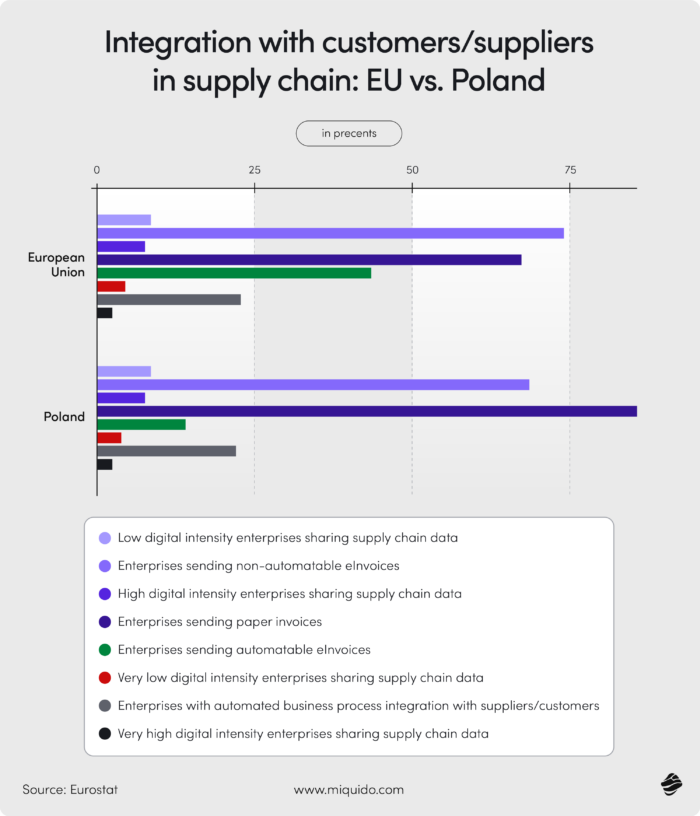
Integration with clients and suppliers: The new standard of efficiency
Manufacturing services supply chain automation brings tangible results. Companies with end-to-end automation report a 40% reduction in order fulfillment time and a 20% drop in operational costs. Seamless digital communication between companies, customers, and suppliers leads to:
- More accurate production planning
- Reduced inventory holding costs
- Faster reaction to sudden market shifts
At the same time, it eliminates problems such as:
- Manual data entry errors
- Delays caused by fragmented systems
- Misaligned inventory levels and order mismatches
Thanks to the integration of ERP and CRM systems, manufacturers can ensure a joined up manufacturing process, providing dynamic responses to order changes and optimized workflows across the entire production process.
Despite a growing awareness of the importance of these enhancements in Poland, the numbers tell a sobering story: 40% of manufacturers still rely on manual information exchange, resulting in extended order cycles, wasted resources, and inefficient production processes.
Integrated systems to manufacturing services: challenges and opportunities analysis
Today, maintaining product quality, hitting delivery targets, and meeting client expectations all depend on one thing: automation powered by cloud computing and connected technologies.
More and more EU manufacturers recognize this shift. But while the vision is shared, the pace of execution varies widely across regions. So what’s slowing some companies down, and where can they pick up speed?
Fragmented IT systems = fragmented operations
Think of your business like a relay race. If each runner is on a different track, passing the baton becomes chaos. That’s what happens when manufacturers rely on isolated IT systems for production, logistics, and sales. These siloed platforms don’t communicate in real time, leading to mismatched inventory data, misallocated resources, and painfully slow decision-making.
Opportunity:
Break down the silos. Integrated IT ecosystems manufacturing technologies link systems across departments, enabling real-time data exchange and better operational alignment.
Disconnected supply chains stall progress
For manufacturers working across borders, digital fragmentation doesn’t stop at the factory gate. Non-standard communication protocols, incompatible systems, and manual data conversions between partners cause ripple effects: delayed shipments, lost visibility, and supply chain headaches that automation should have solved by now.
Opportunity:
Streamline the digital backbone. Automated processes, standardizing communication tools and investing in interoperable platforms accelerates collaboration and removes bottlenecks.
AI and ML: powerful—but still underused
Artificial Intelligence and Machine Learning aren’t just buzzwords – they’re catalysts. Predictive maintenance, dynamic scheduling, real-time demand forecasting—these aren’t future features; they’re today’s competitive edge. Yet adoption remains surprisingly low. In Poland, only 20% of companies analyze data in real time, missing a major chance to boost responsiveness and growth.
Opportunity:
Unlock hidden potential. Companies that embrace AI and ML in their operations report productivity gains of up to 30%.
Leveraging succesful digital integration with custom software approach
As manufacturers confront increasing complexity in supply chains, data management, and production planning, one truth becomes clear: off-the-shelf solutions often fall short. They may handle isolated functions, but rarely deliver the deep integration and strategic flexibility that modern manufacturing demands. That’s where custom manufacturing software makes a difference.
Unified systems that actually work together
A software house specializing in digital transformation can connect ERP, CRM, BI, and SCM systems into a single, coherent environment. No more juggling between disconnected tools or re-entering the same data across platforms – this kind of custom integration breaks down silos, enabling seamless information exchange that powers faster, smarter decisions.
Smarter, more predictive supply chains
With AI and big data, software tailored to your operations can anticipate disruptions before they impact your factory floor. Dynamic production scheduling, real-time logistics updates, and automated inventory optimization transform supply chain chaos into a controlled, data-driven system. For companies managing complex value chains, this can be a game-changer – especially when product life cycle begins with razor-thin delivery margins.
Standards that scale with you
Custom solutions can be built with an API-first approach, ensuring effortless communication with suppliers, partners, and global SCM platforms. Instead of bending your business to fit someone else’s template, you build tools that fit the reality of your production process – today and tomorrow.
At Miquido, you can integrate your factory processes in an custom approach, maximizing your benefits. Bring various AI use cases in manufacturing into life on your factory floor, streamlining your internal and external processes. Some innovations can start generating savings in just few weeks, especially if you choose our AI Kickstarter framework. Let’s discuss your case!
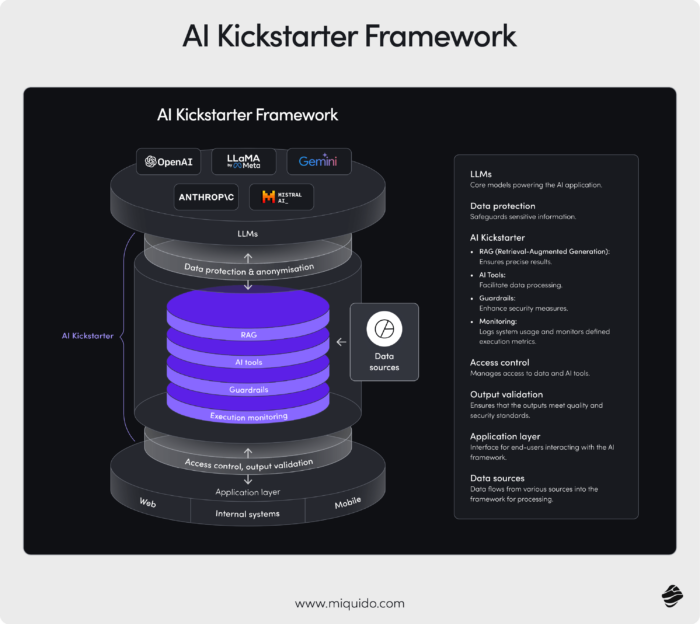